What?
Passivhaus is a tried and tested design principle based on sound building physics, its aim is to achieve a healthy, comfortable and stable environment for building occupants. The concept focuses on reducing energy usage, rather than meeting demand by using renewables.
All levels of the standards focus on the overall building performance with the latter two pushing harder and moving towards a ‘power plant methodology’ where the building starts to generate energy rather than simply consume it. EnerPHit is a retrofit standard with some slight reductions on the Classic criteria
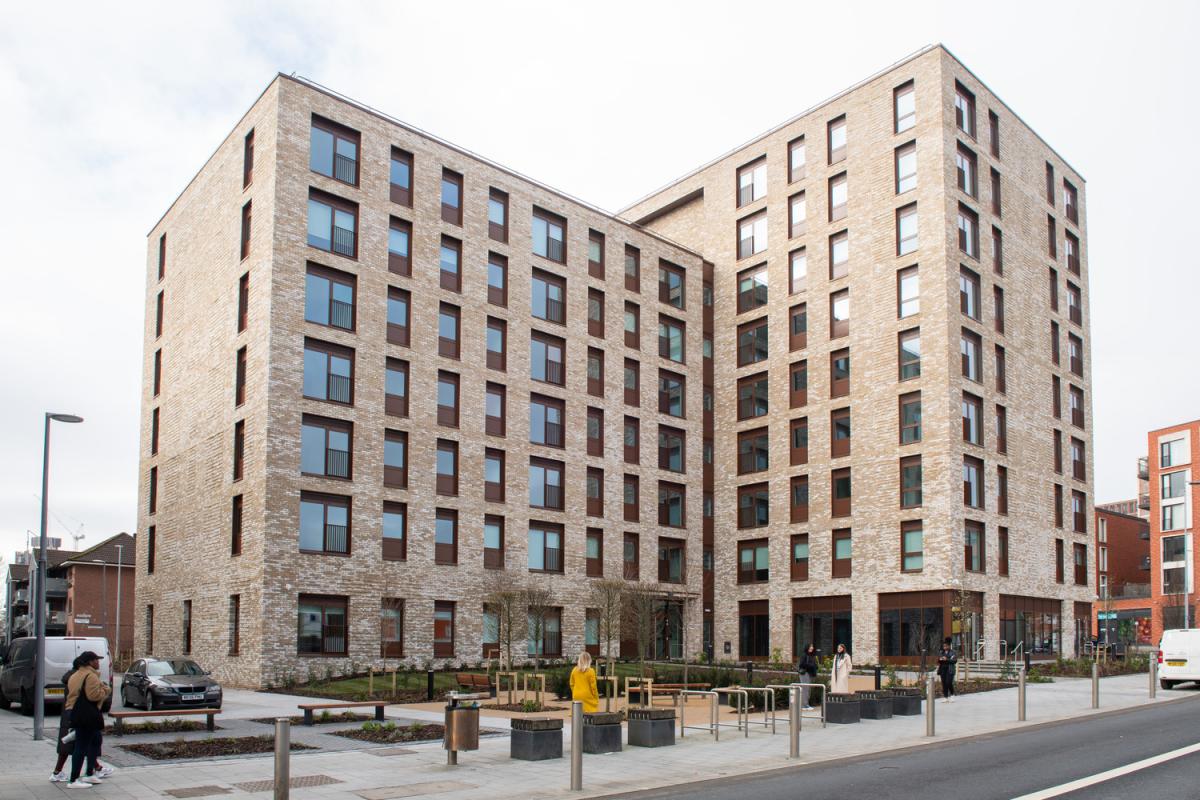
Why?
Passivhaus schemes achieve excellent thermal comfort, very low energy demands, and high levels of insulation and airtightness to provide high comfort and health for occupants. Residents benefit from:
- Low energy demand – homes use up to 70-90% less energy than traditional housing stock.
- Low household bills
- Reduced rent arrears
- High levels of occupant comfort
- Improved resilience
- Longer fabric lifespan
- Little or no gap in performance
- Future Homes compliance
- A route to Net Zero
How?
The Passivhaus Planning Package (PHPP) is used to assess the energy efficiency of a building through the conventions of the Passivhaus principles.
A PHPP calculation needs to be undertaken by a Passivhaus Consultant for each building. Modelling is carried out at the end of RIBA stages 2, 3, 4 and 5 to check the building is meeting the required criteria as it develops. As architects our objective is to simplify the architectural detailing to pre-empt potential site interface issues. To do this we work very closely with contractors and their supply chain to incorporate the following in the design:
- The “form heat loss factor” (the area of external envelope through which heat will escape compared to the area of usable internal floor area) impacts the overall energy efficiency of the building. The better this ratio is the more economical the solution.
- The area of glazing, to carefully balance solar gain and minimise overheating.
- The MVHR units need to be in close proximity of an external wall to limit heat loss from the intake and exhaust ductwork.
- A continuous thermal envelope and limit thermal bridging. Unheated spaces (such as plant and bin stores) should be grouped or sited outside of the building to keep the thermal line as compact as possible.
- A continuous air tightness line
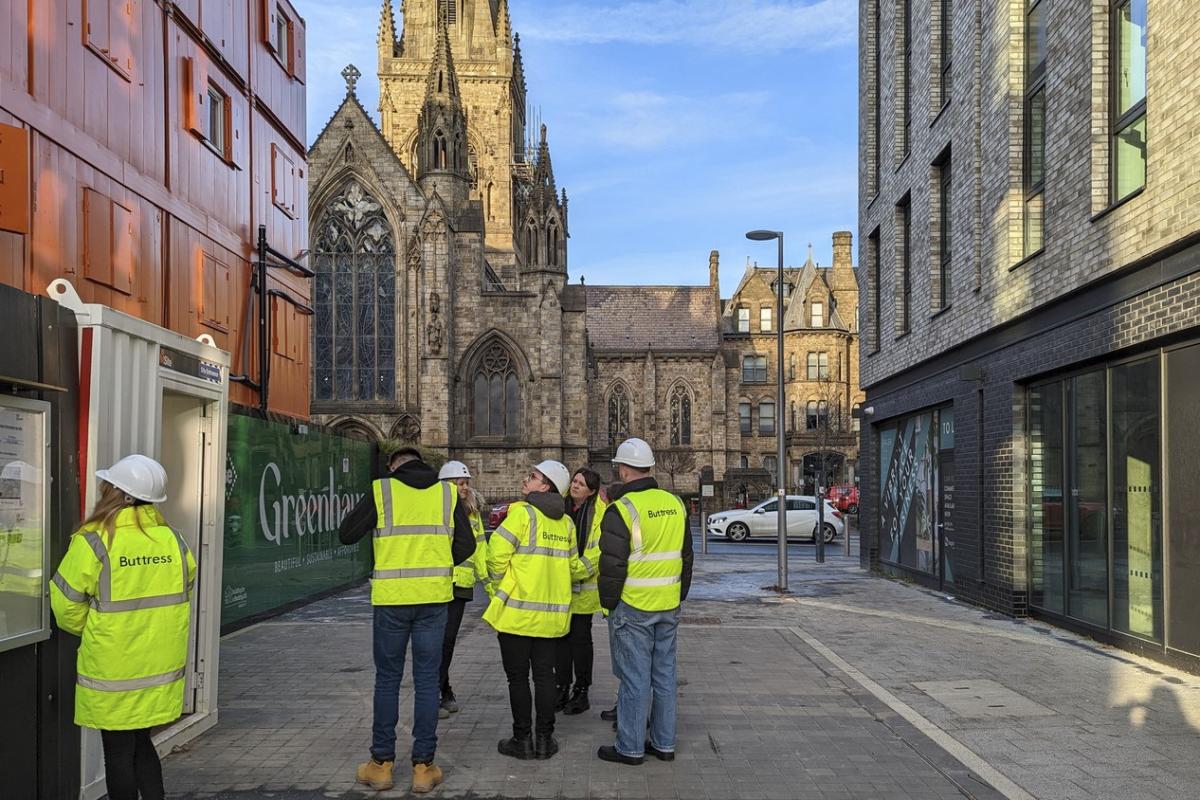
Cost?
The extra cost uplift associated with building to the Passivhaus standard in the UK is around 10% reducing to 4% with further development of skills, expertise and supply chain maturity.
It is important to note that when Passivhaus is adopted from the very start of a project it will also drive efficiency improvements through early design decisions relating to the building form, window design and then later simplification of the detailed design.
These additional costs result in a better quality product, with lower running costs, lower maintenance costs and a higher capital value.
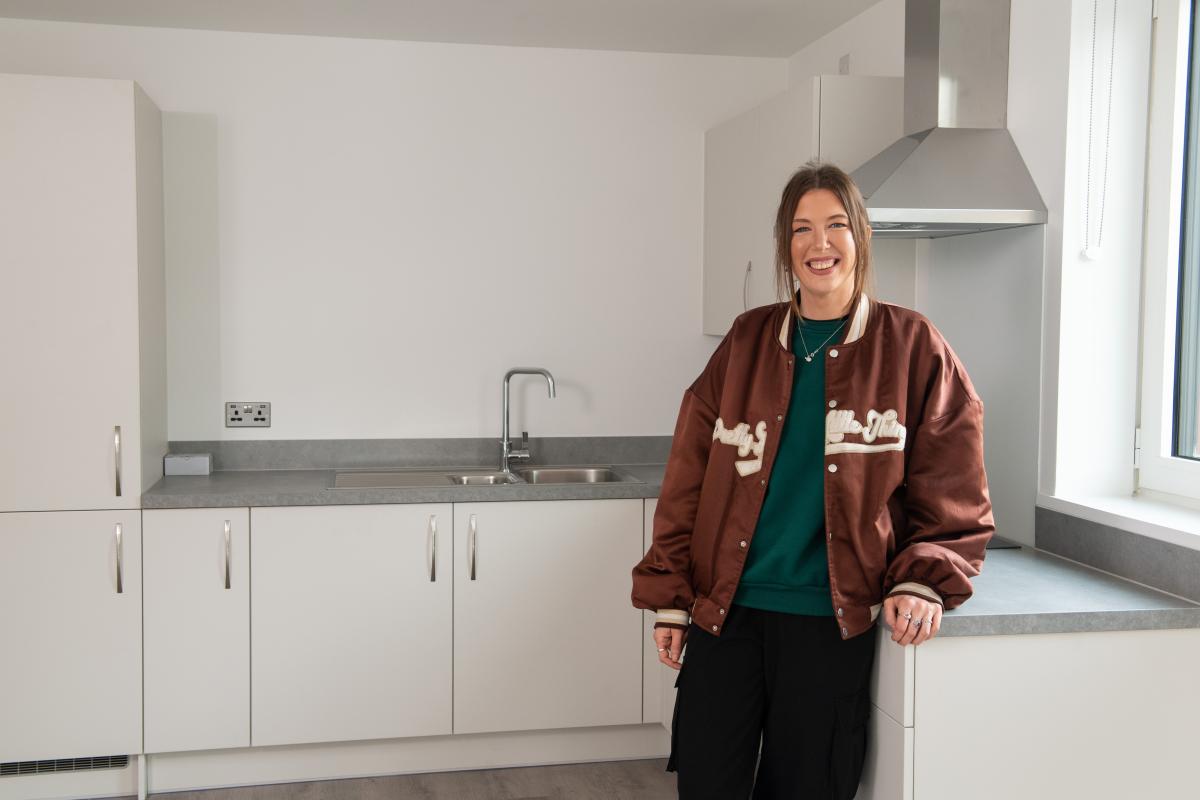
Certification
Every Passivhaus project that aims to be certified requires a Passivhaus designer / consultant and an independent certifier.
The certifier undertakes an initial review at stage 3 and a design review at stage 4. During Stage 5 a construction review is undertaken including site inspections and quality insurance.
It is essential to work closely with the contractors to ensure installation quality and test airtightness using a mock up. This will highlight areas that need addressing before work starts on the main build and avoid costly defects.
Methodical planning is required to ensure the final As Built Assessment and certification align with practical completion.
A considerable amount of the Passivhaus cost uplift is apportioned to the certification process.
It is possible to design a building using the PHPP to Passivhaus Principles. However without the rigourous certification process there is no guarantee that the constructed building will meet the design stage results.
AECB CarbonLite or Retrofit standards also use the PHPP and provide an alternative certification route with less stringent criteria
More on Passivhaus
Greenhaus completes
The largest Passivhaus affordable housing scheme in the North West completes in Salford.
Buttress' Alison Haigh, Certified Passivhaus Consultant
Congratulations to Buttress Associate, Alison Haigh, who has achieved becoming a Certified Passivhaus Consultant.
A passion for Passivhaus
Buttress' Alison Haigh a Passivhaus certified consultant, and Leeds studio lead, James Lewis outline the benefits and challenges of designing Passivhaus residential schemes.