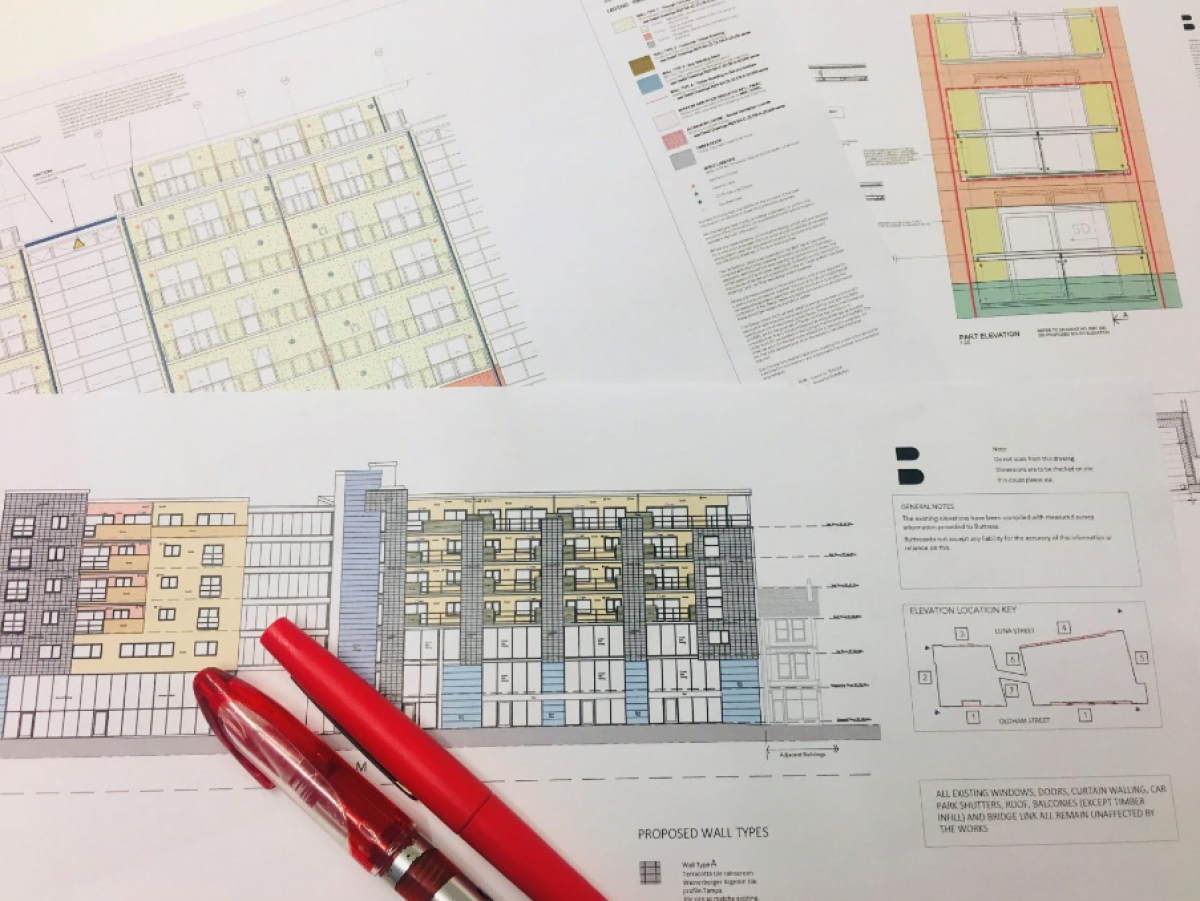
With hundreds of buildings across the country requiring recladding, Managing Director, Gavin Sorby, examines how the industry needs to evolve to meet this challenge and discusses our approach to these projects.
We occupy a post-Grenfell world. Expectations around the performance of cladding materials and external walls have changed profoundly, and the effects will be felt for many years to come.
The heavily oversubscribed Building Safety Fund was set up to help address buildings that require re-cladding, but perhaps did not anticipate how the mortgage and insurance market would respond to the changes in Building Regulations post-Grenfell.
Mortgage companies are unwilling to lend until issues relating to cladding have been addressed, and a EWS1 form issued with owners of even relatively new apartments now unable to sell their properties until expensive re-cladding work is completed. Insurance companies are also adding pressure by hiking premiums or removing cover for buildings that have not been brought up to the current regulations.
The EWS1 forms were originally intended to certify that a building achieved a reasonable level of fire safety and to apply only to buildings over 18m high with cladding to external walls. In some cases, lenders are now requiring an EWS1 for low rise houses, with some assessors requiring full compliance with current Building Regulations.
When work is required; how it can be funded is far from certain. In some cases, leaseholders are required to personally fund the building work with increases in service charges as high as 15 times their normal cost.
The Building Safety Fund has cut-off dates by which tender returns must be submitted. Those buildings that are not funded when the bar drops face an indeterminate future with residents’ lives being put on hold. It is not yet certain what provision, if any, will be made for any schemes that are not sufficiently advanced to hit the Government deadline. There is talk of a possible extension, additional monies, or a low/zero interest loan scheme, to help support owners and tenants fund the works but clarity on the future of the fund is yet to be gained.
As a practice, we have been involved in a number of projects to address issues with cladding. However, navigating the developing legislation and guidance can prove challenging with inconsistent interpretation.
Many buildings procured through D&B contracts have no available drawings, no O & M manuals, and no Health and Safety files. In these cases, we have started from scratch using measured surveys to piece together an existing set of details based on an intrusive survey. When we are able to obtain original concept design drawings, they are often different from construction drawings, and typically neither set of drawings accurately represents the reality of what is physically there. As a solution to this, we have carried out further intrusive surveys and commissioned measured surveys to piece together a set of base drawings. Developing this base set of details has been key to minimising financial risk at tender stage.
To date, most building owners have sought to use the Building Safety Fund, but it is not uncommon to uncover other building defects and fire separation issues that are not covered by the Fund. In one case, the fire separation between floors had been compromised just to achieve a recessed curtain track. Typically there is no funding available to deal with these matters and they are left as residual risks for the management company to address.
As a practice, we have now researched a range of remedial approaches to deal with ACM and HPL panels, zinc and copper cladding on plywood and insulated render systems. The market has not yet matured in the UK so options can be limited, particularly when existing finishes need to be matched for planning purposes.
It is usually possible to make the necessary changes to these buildings without the need for planning consent. Although we have encountered one building required to achieved BREEAM excellent as a planning condition which was highly insulated and stuffed full of combustible foam. The non-combustible insulation, however, occupies more space than the original foam. In these cases, there needs to be a pay-off between retaining the design integrity and resolving the technical issues as required.
Everyone should feel safe within their home and it is right to put safety at the fore. That said, it is clear that more lessons need to be learnt. Echoing the Hackitt Review’s reference to a ‘golden thread’ that runs through all phases of design, construction and occupation, in order to bring about real change, we - as an industry - have a responsibility to work together, share knowledge, and effectively communicate to ensure that earlier mistakes are not repeated.
To find out more about our recladding work and to speak to a member of the team get in touch below.